In our previous blog, we highlighted key obstacles currently hindering the evolution of sustainable aviation fuels, stunting our reach for carbon-neutrality by 2050. The most important being a scalable biofuel form equivalent to that of Jet A. SAF’s objective is to mimic Jet A fuel characteristics so airliners and pilots are relieved from managing varying levels of fuel performance. Whether it is petroleum or biologically driven, it all performs the same. But how do we achieve this and why is it important? To reach Jet A competition, and hopefully total replacement, we must make a fuel that is most commercially viable.
To produce a complete fuel, we must first create their components, all differing in compounds and molecular make-up to reach the highest level of energy-density, lubrication, and performance at cost parity. In other words, more bang for our buck. The flexibility offered by biofuels allows R&D to achieve these fuel specificities while upholding ASTM standards poses a significant advantage, especially allowing for various approaches in biomanufacturing9. United Airlines Ventures being the lead investment player in this new campaign is investing in several companies to produce over 3 billion gallons of SAF for future use1. In addition to UAV’s efforts, funding sourced from private-public capital partnerships and government entities have catalyzed SAF initiatives, kickstarting several unique production pathways that have burst into the biofuel space as novel technologies evolved from existing methods, primarily bio-fermentation. In this blog post, we explore four bio-fermentation pathways—sugar fermentation, lipid fermentation, lignocellulosic fermentation, and syngas fermentation—and their biomanufacturing potential for scalable SAF production.
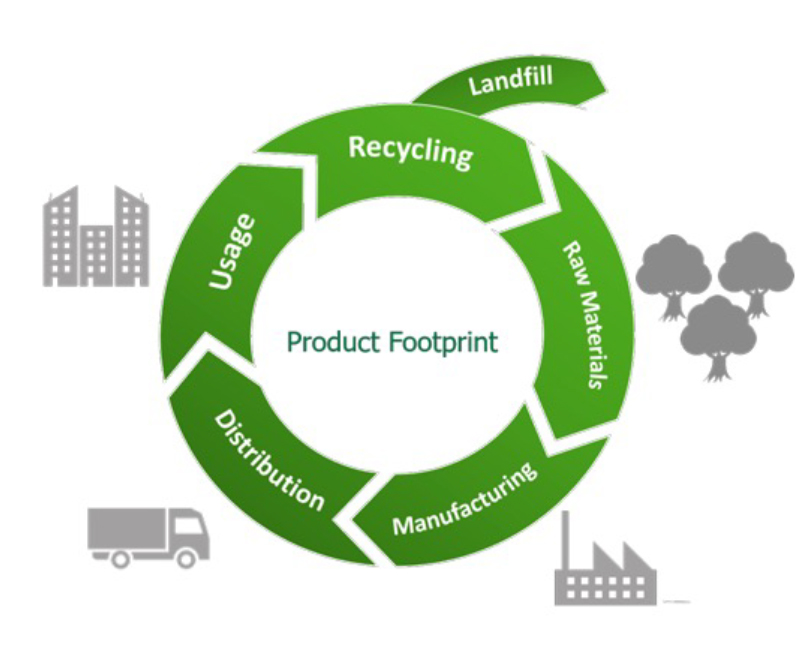
Bio-fermentation, a key process in SAF biotechnology, follows a circular pattern that harnesses the metabolic capabilities of microorganisms, such as bacteria, yeast, or fungi, to convert organic materials into valuable products. This natural process has been utilized for centuries in various applications, including the production of food, beverages, and various other consumables. Advancements in SAF production continue to utilize this basic science but in a way that further caters to cost effectiveness, decarbonization, and biofuel potency. All while reducing lifecycle greenhouse gas emissions by up to 80% compared to conventional jet fuels1. Through various fermentation pathways, such as sugar fermentation, lignocellulosic fermentation, lipid fermentation, and gasification, companies specializing in bio-manufacturing are making significant strides in SAF production3. These innovative ventures leverage scientific expertise, genetic engineering, and optimize basic fermentation processes to convert diverse organic sources into biofuel components. Bio-fermentation for SAF production involves several key biological steps, beginning with feedstock preparation, where different types of feedstocks, such as sugars, lignocellulosic biomass, algae, or glycerol, are obtained. Specific microorganisms, such as bacteria, fungi, or yeast, are then chosen based on their ability to efficiently convert the chosen feedstock into fuel precursors where the application of precise engineering techniques are employed to enhance their performance output. The selected microorganisms are then cultivated in bioreactors under controlled conditions where the feedstock is introduced as a primary carbon source. The process of fermenting this organic carbon source relies heavily on nutrient availability to create a conducive environment for microorganisms to enzymatically catabolize complex structural molecules into glucose (sugars). These sugars are then fermented by bacteria using metabolic processes to yield compounds to create a desired drop-in fuel component depending on fuel mixture requirements and regulations3.
SAF Optimizing Fermentation Pathways
Sugar Fermentation: Fueling the Future with Microbes
Sugar fermentation, utilizing microorganisms such as bacteria, involves the conversion of carbon rich feedstocks and biomasses (ex. food and crop waste) into glucose-based biofuel components. After fermentation, the alcohol byproduct is distilled, purified, and blended to meet SAF engine specifications. This process offers the advantages of utilizing renewable biomass feedstocks and achieving high ethanol yields, but ethanol has recently come to be an inefficient fuel stock component, therefore necessitating alternative sugar-based fuel compounds. One notable company in this field is Visolis, renowned for its expertise in synthetic biology is employing advanced genetic engineering techniques to optimize microorganisms for efficient sugar utilization to produce an ethanol alternative2. Visolis fine-tunes metabolic pathways and enhances fermentation processes to achieve high yields of SAF precursors, specifically isoprenol6. Isoprene acts as a key monomer for rubber production when combined with specific compounds but if not polymerized, isoprene functions as a very useful fuel additive4. With appropriate chemical treatment, isoprene can be converted into a highly efficient drop-in fuel source making it a valuable option for enhancing fuel quality, characterized by its high energy density, jet engine compatibility, and low viscosity. It is worth noting that compounds used in lubricants, fuels, solvents, sealants, paints, and coatings are remarkably similar, often differing only in blend composition or polymerization for specific applications2. This shared chemistry allows biofuel manufacturing to tap into a promising space where the need for initial compound refinement is eliminated, and the desired product can be directly synthesized. The scalability of sugar fermentation lies in the ability to cultivate and manipulate microorganisms in large-scale fermentation systems. This biomanufacturing approach enables the production of SAF on a commercial scale, meeting the increasing demand for sustainable aviation fuels9.
Lipid Fermentation: Nature’s Bounty
Lipids, which are fats or oils, can be extracted from various feedstocks like algae, waste oils, or oil-dense crops. The biopathway of lipid fermentation then converts the extracted lipids into fatty acid methyl esters (FAMEs) suitable for sustainable aviation fuel. The process involves enzymatic hydrolysis of lipids, followed by the metabolism of fatty acids by microorganisms like bacteria or yeast. Through esterification, the fatty acids react with alcohol, typically methanol, forming FAMEs11. This precise control and optimization enable the production of FAMEs with properties comparable to conventional jet fuel. Studies have shown that lipid fermentation can achieve high lipid content in algae, reaching up to 50% of dry biomass8. Additionally, life cycle assessments indicate an approximate 80% reduction in carbon emissions compared to traditional jet fuel when sourced from lipid-based feedstock 9. Oxy, short for Occidental Petroleum Corporation, is an energy company engaged in the development of SAF through lipid fermentation to produce biogas resources. Oxy is focused on converting lipids from various feedstocks into renewable hydrocarbons, such as FAMEs, which can be used as drop-in replacements for conventional jet fuel7. In addition to Oxy, Viridos, a leading synthetic biology company, actively optimizes lipid cultivation of high lipid-producing algae strains. By implementing innovative refining methods, such as photobioreactors, Viridos maximizes algae growth and lipid accumulation for subsequent conversion into SAF11. Supporting data from their research showcases increased lipid productivity and the successful extraction of lipids from algae biomass, demonstrating the potential of algae fermentation as a sustainable route for SAF. Innovations in fermentation process optimization and genetic engineering have unlocked remarkable scalability. Bioreactor systems and cultivation strategies have been developed to enhance lipid accumulation, paving way for their large-scale production5,8.
Lignocellulosic Fermentation: Harnessing Nature’s Complexity
Lignocellulosic biomass, such as agricultural residues, forestry waste, or dedicated energy crops, contains complex carbohydrates like cellulose and hemicellulose. Through a series of pretreatment and hydrolysis steps similar to sugar fermentation, complex lignin-based plant carbohydrates are broken down into simple sugars. Advanced pretreatment techniques and enzymatic hydrolysis enhance the accessibility of these carbohydrates so microorganisms like bacteria or yeast can then ferment sugars into hydrocarbon compounds suitable for SAF production. Research has reported sugar yields ranging from 300 to 400 g/kg of biomass which offers up a significant source for SAF synthetization3. A research institute modifying the biomanufacturing of this process is the Joint BioEnergy Institute (JBEI). As a DOE funded institution, JBEI is currently focusing on developing advanced biofuels and bioproducts from sustainably sourced biomass with high energy availability without relying on fuel-designated crops. JBEI conducts research on various fermentation pathways, including lignocellulosic fermentation, and is working on developing microbial strains and bioprocesses to efficiently streamline the conversion of lignocellulosic biomasses into SAF3. Life cycle assessment studies utilizing lignocellulosic fermentation indicate up to an 85% reduction in GHG emissions compared to conventional jet fuel3. With advances in bioreactor design and microbial engineering, lignocellulosic fermentation offers an attractive and scalable pathway for SAF production. Biomanufacturing strategies like simultaneous saccharification and fermentation (SSF) and consolidated bioprocessing (CBP) streamline processes, improving conversion efficiencies and supporting the industry’s efforts to meet the growing demand for sustainable aviation fuels3,9.
Syngas Fermentation: Carbon-Rich Gases
The final fermentation pathway we will cover is gasification of feedstocks to form syngas. Syngas fermentation involves converting mixtures of carbon monoxide and hydrogen obtained from sources like biomass gasification, into valuable compounds such as ethanol or butanol through microbial fermentation and has emerged as a valuable precursor and versatile intermediate for SAF synthesis7. One pathway involves the Fischer-Tropsch (FT) synthesis, where syngas is converted into liquid hydrocarbon fuels to suit aviation energy standards10. Another prominent approach is the direct hydrogenation of syngas, yielding high-purity hydrogen gas that can be combined with carbon from biomass or captured CO2 for drop-in jet fuel production. Industry leaders, such as LanzaJet and Cemvita Factory, are actively utilizing syngas-derived hydrogen for SAF production. Lanza’s emphasis on syngas fermentation revolves around specialized microorganisms capable of metabolizing carbon monoxide and hydrogen present in syngas12. Similarly Cemvita Factory, specializing in biologically inspired engineering solutions, are currently developing sustainable and scalable biomanufacturing processes that apply syngas fermentation by creating microbial systems capable of converting carbon waste and CO2 emissions into valuable chemicals and hydrocarbon compounds for SAF biomanufacturing. Research has demonstrated fuel yields of 0.5-1g for every gram of CO2 consumed and up to 80% reduction in carbon emissions compared to conventional jet fuel10. With advances in bioreactor design, gas-liquid mass transfer, and strain engineering, syngas fermentation can be conducted in large-scale systems, especially with biomanufacturing strategies such as continuous fermentation or immobilized cell systems, to maximize efficiency and cost-effectiveness12. Syngas fermentation presents an exciting pathway for scalable SAF production, leveraging carbon-rich gases.
By incorporating these scientific details, it becomes evident that these bio-fermentation pathways hold tremendous potential to produce sustainable aviation fuels, showcasing their efficiency and environmental benefits. In addition to promising science, the presence of established industry leaders partnering with innovative start-ups underscores the significance of collaboration. Notable players in the field, such as Cemvita Factory, Oxy Ventures, Visolis, United Airlines Ventures, and various government entities are actively contributing to the scientific advancements and commercialization of bio-fermentation processes for sustainable aviation fuel.
This collective effort fosters an environment of shared knowledge and accelerated progress showcasing potential to overcome obstacles and drive the widespread adoption of SAF across our domestic and global bioeconomy. It is important to acknowledge that at this stage, it is difficult to predict which specific pathway or combination of pathways will emerge as the dominant solution. While specific winners of the bio-fermentation race are yet to be determined, the involvement of major players and the spirit of collaboration provide reasons for optimism. The journey towards sustainable aviation fuel production is underway, and with each step forward, we move closer to a more environmentally friendly and sustainable aviation industry to ensure a greener and cleaner sky for generations to come.
In our third and final installment of our SAF blog series, we will discuss how the scalability of these scientific approaches will fundamentally impact our bioeconomy by means of improving national security and creating a dominant supply chain, going beyond GHG emission reductions.
References:
1. United Airlines Sustainable Aviation Fuel (SAF) Program- https://www.united.com/en/us/fly/company/responsibility/sustainable-aviation-fuel.html\
2. Visolis/Ginkgo tie-up for bio-isoprene for making tyres/aviation fuel- https://rubberjournalasia.com/visolis-ginkgo-tie-up-for-bio-isoprene-for-making-tyres-aviation-fuel/
3. Sustainable Aviation Fuels at JBEI- https://caafi.org/resources/pdf/CAAFI_Webinar_JBEI_Simmons_Feb_2022.pdf
4. Bio-based high-purity isoprene through high-yield technology- https://cordis.europa.eu/project/id/663118
5. Sustainable Aviation Fuels From Algae- https://www.wur.nl/en/project/sustainable-aviation-fuels-from-algae.htm
6. Engineering S. cerevisiae to Produce Isoprenol for Sustainable Aviation Fuel and Chemicals 2020-086- https://ipo.lbl.gov/engineering-s-cerevisiae-for-isoprenol-production-at-industrial-scale/
7. Turning Carbon Dioxide into Sustainable Fuel- https://www.prnewswire.com/news-releases/turning-carbon-dioxide-into-sustainable-fuel-united-and-oxy-low-carbon-ventures-announce-collaboration-with-biotech-firm-to-create-new-fuel-sources-301512378.html
8. From Wet Waste to Flight: Scientists Announce Fast-Track Solution for Net-Zero-Carbon Sustainable Aviation Fuel- https://www.nrel.gov/news/program/2021/from-wet-waste-to-flight-scientists-announce-fast-track-solution-for-net-zero-carbon-sustainable-aviation-fuel.html
9. SAF Grand Challenge Roadmap- https://www.energy.gov/sites/default/files/2022-09/beto-saf-gc-roadmap-report-sept-2022.pdf
10. Gas fermentation for microbial sustainable aviation fuel production- https://www.publish.csiro.au/ma/pdf/MA23008
11. Life-Cycle Analysis Shows Potential for Almost 70% Greenhouse Gas Emissions Reductions of Renewable Diesel from Algae Fractionation Compared to Conventional Diesel- https://www.energy.gov/eere/bioenergy/articles/life-cycle-analysis-shows-potential-almost-70-greenhouse-gas-emissions
12. LanzaJet- https://www.lanzajet.com/what-we-do/
Recent Comments